LT Energy coupling device
The Energy coupling device is a collection of multiple connection types on a single frame or housing, and can be configured according to specific specifications. It can meet the multi-function and frequent plug requirements, integrated the power, signal, data, fiber, liquid and pneumatic, etc. Suitable for applications which need combine electrical, power and pneumatic connections together.
.png)
High stability; High reliability
|
.png)
Ultra-high plug-life
|
.png)
Strong current carrying capacity
|
.png)
Strong resistance to vibration and impact
|
.png)
Φ 1.6 Signal Module
Table
 |
Mechanical parameters: |
|
Insertion force [N] |
1 |
Pullout force [N] |
0.5 |
Mechanical life [times] |
≥100000 |
Jack type |
Springtac TM |
Electrical parameters: |
|
Maximum continuous current [A] |
13 |
Instantaneous current [A] |
25 |
Contact resistance (max) [mΩ] |
25 |
Wire specification [mm²] |
1.5 |
Material/Coating |
Copper alloy/gold plating |
Environmental protection requirements |
RoHS 2.0 |
|
Φ 4 Power Module
Table
.png) |
Mechanical parameters: |
|
Insertion force [N] |
6 |
Pullout force [N] |
3 |
Mechanical life [times] |
≥100000 |
Jack type |
Springtac TM |
Electrical parameters: |
|
Maximum continuous current [A] |
25 |
Instantaneous current [A] |
50 |
Contact resistance (max) [mΩ] |
0,8 |
Wire specification [mm²] |
4 |
Material/Coating |
Copper alloy/gold plating |
Environmental protection requirements |
RoHS 2.0 |
|
Φ 8 Power Module
Tabela
.png) |
Mechanical parameters: |
|
Insertion force [N] |
25 |
Pullout force [N] |
15 |
Mechanical life [times] |
≥100000 |
Jack type |
Springtac TM |
Electrical parameters: |
|
Maximum continuous current [A] |
105 |
Instantaneous current [A] |
210 |
Contact resistance (max) [mΩ] |
0,35 |
Wire specification [mm²] |
35 |
Material/Coating |
Copper alloy/gold plating |
Environmental protection requirements |
RoHS 2.0 |
|
Φ 14 Power Module
Tabela
.png) |
Mechanical parameters: |
|
Insertion force [N] |
40 |
Pullout force [N] |
30 |
Mechanical life [times] |
≥100000 |
Jack type |
Springtac TM |
Electrical parameters: |
|
Maximum continuous current [A] |
400 |
Instantaneous current [A] |
40 |
Contact resistance (max) [mΩ] |
135 |
Wire specification [mm²] |
50/70 |
Material/Coating |
Copper alloy/gold plating |
Environmental protection requirements |
RoHS 2.0 |
|
1000Mbps Network Module
Tabela
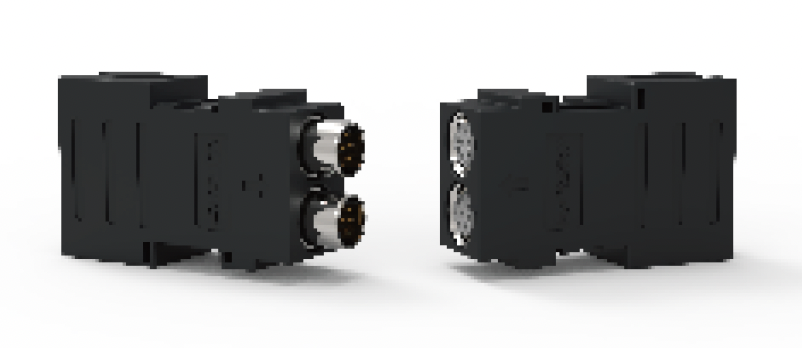 |
Termination methods |
Welded plate |
Mechanical property: |
|
Mechanical life [times] |
50000 |
Vibration and shock |
GB/T 21563 Class I Level B requirements |
Electrical property: |
|
Rated voltage |
500V |
Rated current |
4A |
Voltage resistance |
650V |
Contact resistance |
≤8mΩ |
Work temperature |
-40 °C ~ 125 °C |
Network performance |
1000 Mbps |
Environmental protection requirements |
RoHS 2.0 |
|
Φ3 Two-core pneumatic&liquid module
Table
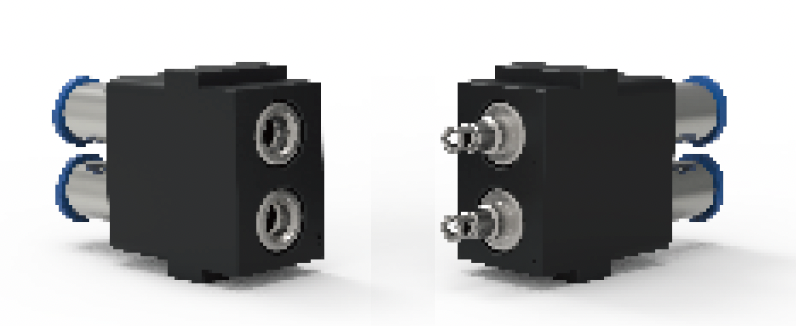 |
Used for coupling compressed air and coolant |
|
Poles number |
2 |
Diameter [mm] |
3 |
Support block material |
POM |
Max working pressure [bar] |
15 |
Min working pressure [mbar] |
14 |
Work temperature [°C] |
-15~90 |
Sealing material |
NBR |
Pipe outer diameter [mm] |
6 |
Mechanical life [times] |
≥100000 |
|
LT-F31-BI11 Energy Connector
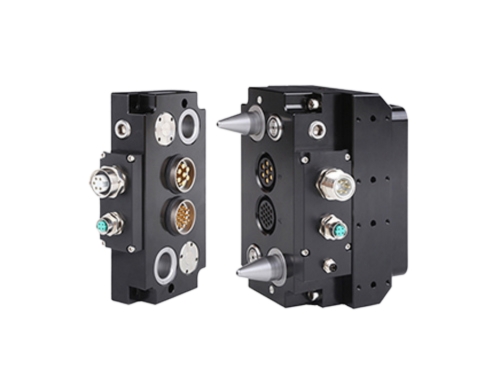 |
Robot side PO: 1670 |
Tool side PO: 1671 |
Provide energy connection between master station and slave station. |
With X, Y, Z directional floating performance, eliminate docking error. |
Modular design of medium unit, more flexible configuration. |
Pass through medium such as electric power, data, i/o, air, liquid and other media. |
Integrated tool side in position detection sensor. |
Identification slave station number. |
|
PO |
Model |
Configuration Parameters |
Weight (KG) |
Robot Side |
1670 |
LT-F31-BI11-M |
2*PT3/8 self-sealed pneumatic ports
7/8-5 pin 9A independent bus power supply
M12-4-pin D-coded bus interface
Optional proximity switch
|
0.087 |
Tool Side |
1671 |
LT-F31-BI11-T |
0.068 |
|
Compensation available:
- Compliance (X&Y-Axis): ±4mm
- Compliance (Z-Axis): +2mm
- Rotational Compliance: ±3°
- Min. Coupling Force: ≥1526N
LT-F31C Energy Connector
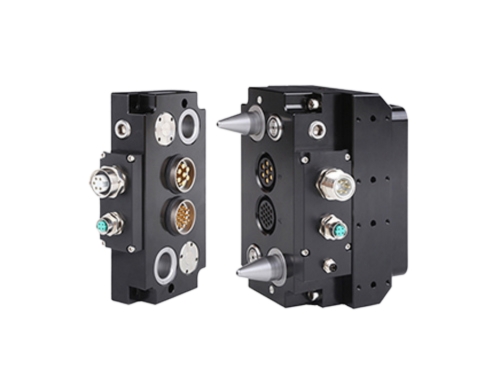 |
Optional max 4 x PT1/2 pneumatic ports or Liquid ports |
Provide energy connection between master station and slave station |
With X, Y, Z directional floating performance, eliminate docking error |
Pass through medium such as electric power, data, i/o, air, liquid and other media |
Integrated tool plate in position detection sensor |
Optional driven way: Servo Motor or Pneumatic |
|
Compensation available:
- Compliance (X&Y-Axis): ±4mm
- Compliance (Z-Axis): +2mm
- Rotational Compliance: ±3°
- Min. Coupling Force: ≥1526N
Optional configuration:
Signal IO: |
Industrial Bus Control: |
Servo motor connector: |
Electrical power: |
Air and liquid module: |
19~130 channel available |
-Profibus
-DeviceNet
-EtherNet
-Profinet
-CC-Link |
Available for ABB, KUKA, Fanuc, Yaskawa Servo motor interface
Servo + signal interface is optional |
7~35 channel available |
1~4 x PT1/2 pneumatic ports or Liquid ports available |
LT-F41 Energy Connector
.jpg) |
Lightweight design, compact structure |
Realize rapid connection of energy media such as current and communication |
With X, Y, Z directional floating performance, eliminate docking error |
Optional servo motor or cylinder drive |
|
Compensation available:
- Compliance (X&Y-Axis): ±4mm
- Compliance (Z-Axis): +2mm
- Rotational Compliance: ±3°
- Min. Coupling Force: ≥1526N
LT-FEC Frame
LT-FEC Frame Specifications
.png) |
Frame float (FEC frame with Q4 ground) |
|
X/Y direction |
±1mm |
Z direction |
±0.2mm |
Floating Angle |
±1° |
Positioning Repeatability |
±0.1mm |
Rail length [mm] |
48/72/96/144 |
|
Φ 4 Ground Pin
Table
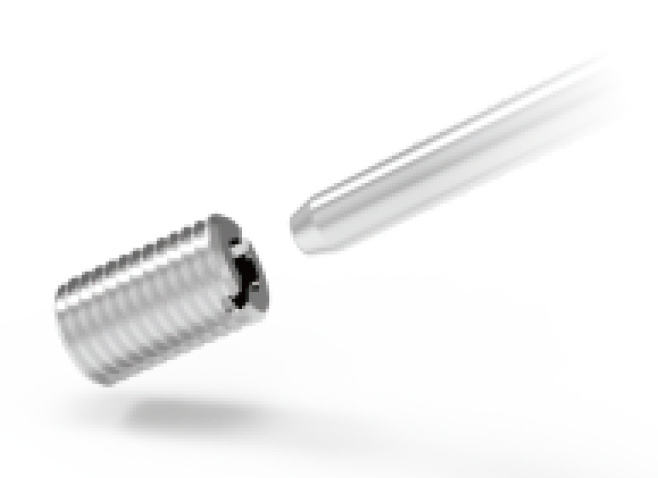 |
Mechanical capacity: |
|
Insertion and extraction force [N] |
4-8 |
Mechanical life [usage times] |
≥100000 |
Work Environment: |
|
Work temperature |
-40°C~+125°C |
Material/Coating/Appearance: |
|
Pinhole parts/terminals |
Copper alloy, plated with silver |
Standard and certification: |
|
Environmental requirement |
RoHS 2.0 |
|
Water&Pneumatic Interface
Tabela
.png) |
Diameter [mm] |
8 |
Max pressure [MPa] |
1.6 |
Connection force without pressure [N] |
150 |
Repulsive cross-sectional area [cm²] |
4.35 |
Service life [million times] |
100 |
|
Hydraulic Interface
Tabela
.png) |
Hydraulic interface |
LTPH08, LTPH08B, LTPH12, LTPH12B |
Diameter [mm] |
LTPH08, LTPH08B: 8; LTPH12, LTPH12B: 12 |
Connection force without pressure [N] |
LTPH08, LTPH08B: 163; LTPH12, LTPH12B: 210 |
Socket/Plug repulsive cross-sectional area [cm²] |
LTPH08, LTPH08B: 2.14; LTPH12, LTPH12B: 4.52 |
Flow [speed 5m/s] [l/min] |
LTPH08, LTPH08B: 16.49; LTPH12, LTPH12 |
Insertion and extraction service life [number] |
≥100000 |
Max pressure [MPa] |
LTPH08: 16; LTPH08B: 25; LTPH12: 16; LTPH12B: 25 |
|